1. Introduction
2. Enamel Plate Condenser
2.1. Structural Design
2.2. Operational Principle
During operation, hot and cold fluids flow on opposite sides of the enamel plates. Heat is transferred from the hot fluid, through the enamel plate, to the cold fluid, thereby achieving the desired cooling or condensation effect.
2.3. Merits
- The relatively straightforward structure simplifies manufacturing and assembly processes, translating to a lower cost.
- Exhibits a certain degree of resistance to corrosion, making it suitable for mildly corrosive media.
2.4. Demerits
2.5. Ideal Applications
3. Enamel Shell and Tube Condenser
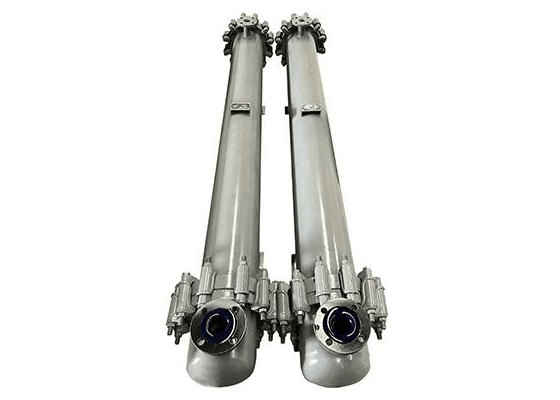
3.1. Structural Configuration
Comprises a shell, tube sheets, and heat exchange tubes arranged in a compact and efficient manner. This design maximizes the available heat exchange area within a confined space.
3.2. Working Mechanism
Hot fluid circulates inside the tubes, while cold fluid surrounds the tubes in the shell. Heat is transferred through the tube walls, leveraging the principle of convection to achieve efficient heat exchange.
3.3. Advantages
- The heat exchange tubes, enameled using a hanging - burning process, boast uniform thickness and high quality, enhancing the overall performance and lifespan of the condenser.
3.4. Disadvantages
- The manufacturing process is intricate and demands advanced techniques and machinery, resulting in a higher production cost compared to the enamel plate condenser.
- The compact tube bundle structure poses challenges during cleaning and maintenance. Internal fouling or blockages can be difficult to address and may require specialized equipment and expertise.
3.5. Suitable Applications
Ideal for industries that demand high heat exchange efficiency, robust pressure resistance, and excellent corrosion resistance. Commonly used in chemical, pharmaceutical, and food processing industries, especially in processes involving high - temperature, high - pressure, and highly corrosive media.
4. Comparative Analysis and Conclusion
When comparing the enamel plate condenser and the enamel shell and tube condenser, it becomes evident that each has its own set of strengths and weaknesses. The plate condenser offers simplicity and cost - effectiveness but falls short in terms of performance and versatility. On the other hand, the shell and tube condenser excels in heat transfer efficiency, durability, and adaptability to harsh conditions, albeit at a higher cost and with more complex maintenance requirements.
In making a selection, it is crucial to consider various factors such as the specific requirements of your industrial process, the nature of the fluids involved, operating conditions (pressure, temperature, vacuum), and budgetary constraints. By carefully weighing these factors, you can make an informed decision and choose the condenser that best aligns with your production goals, ensuring efficient, reliable, and safe heat exchange operations.